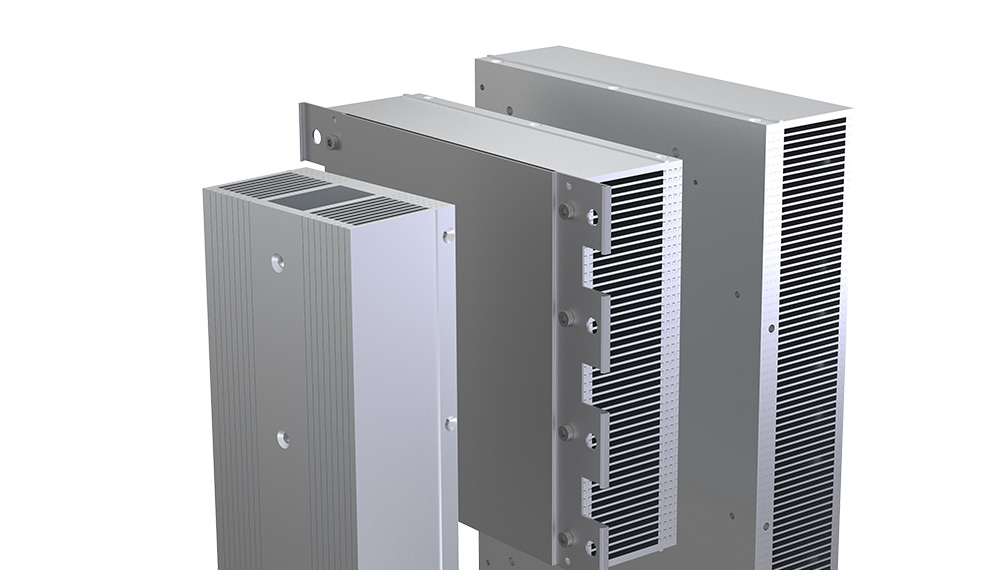
Soldering
Soldering plays a critical role in the production of heat sinks and liquid cooling plates. Various soldering methods, whether precise hard soldering or more flexible soft soldering, allow for adaptive integration of components, creating efficient cooling structures.

Flame Soldering
Flame soldering is a specialized soldering technique used in both soft and hard soldering. The process involves using an open flame to melt the solder material and join the materials to be connected. The choice between soft and hard soldering depends on the specific application requirements. Soft soldering takes place at relatively low temperatures, usually below 450°C, using solder with a low melting point, often based on lead or tin. This typically provides temperature stability up to around 110°C. Soft soldering is suitable for materials with lower melting points, such as copper or aluminum. It is particularly effective when heat sensitivity must be avoided, though the connection strength is lower compared to hard soldering. Hard soldering, on the other hand, is performed at higher temperatures, typically above 450°C, using solder with a higher melting point. This technique creates stronger connections and is suitable for materials with higher melting points, such as stainless steel or copper alloys. However, the higher temperature can cause thermal stress on the materials.
Induction Soldering
Induction soldering is an advanced soldering technique that uses electromagnetic induction to generate heat for the soldering process. Compared to conventional methods such as flame soldering, induction soldering offers precise, efficient, and localized heating, making it particularly suitable for demanding applications. The process begins by running an alternating electric current through a coil placed near the components to be soldered. This coil generates a strong magnetic field that penetrates the metal parts. Eddy currents induced in the materials generate surface heating.
The advantage of induction soldering lies in its ability to generate heat exactly where needed, resulting in faster and more precise soldered connections. This is especially important in applications with sensitive parts or when selective heating is required. Induction soldering also benefits from contactless heating, ensuring that solder paste or solder melts only at predetermined spots.
Resistance Soldering
Resistance soldering is a specialized technique that generates heat for soldering by passing an electric current through the material to be soldered. The process typically involves specialized soldering tongs or electrodes that conduct the current through the solder or solder paste. The heat generated by the material's resistance to the current melts the solder, forming a strong bond between the components. The benefits of resistance soldering include precise heat control and rapid heating of the soldering area. This technique is well-suited for small to medium-sized components requiring targeted heat application. The process also allows for improved control over the soldering temperature.
Vacuum Soldering
Vacuum soldering is a specialized form of soldering conducted under reduced pressure. This method offers precise control over the soldering process. Reducing the ambient pressure lowers the boiling point of the solder, enabling the soldering process to be carried out at lower temperatures and without flux. The vacuum process has several advantages, including reducing the formation of oxides on the surfaces of the materials to be soldered, resulting in high-quality soldered connections.