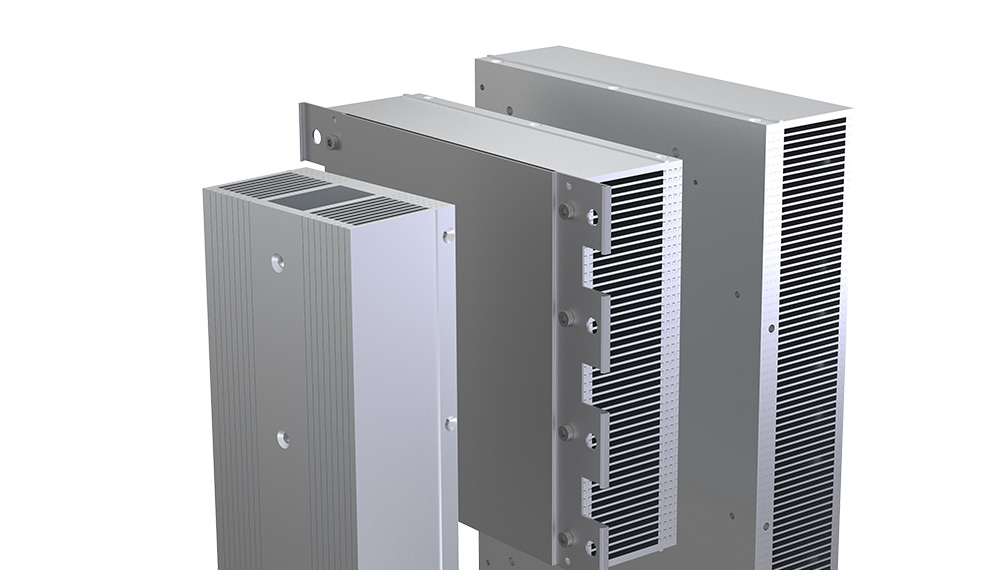
Aluminum
Air and liquid coolers are primarily made of aluminum or copper due to their high thermal conductivity. However, some applications now require stainless steel as the base material due to particularly aggressive environmental conditions.
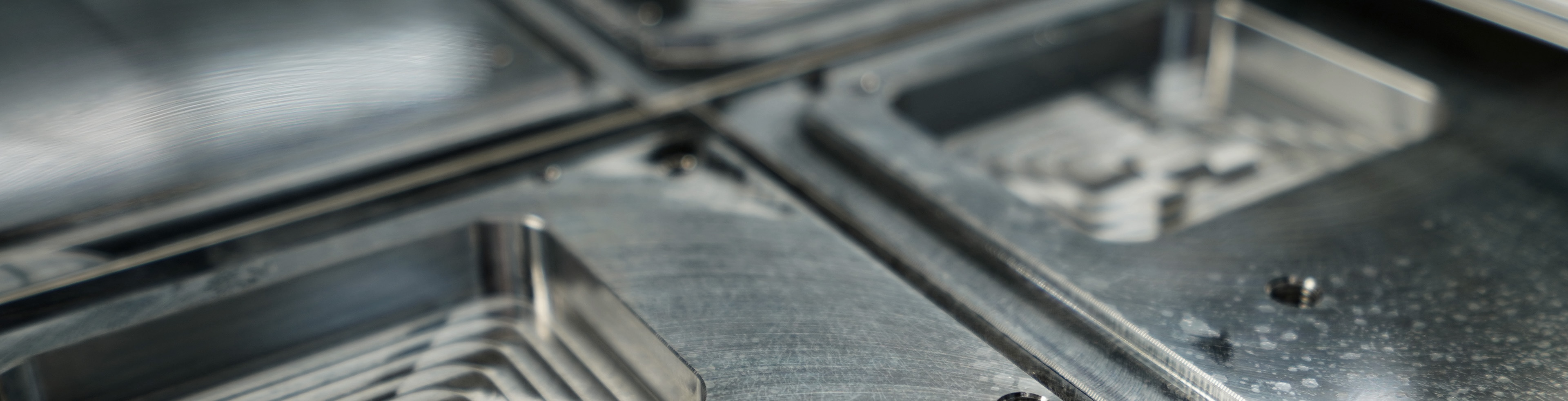
Importance & Advantages
Aluminum is the preferred material for manufacturing heat sinks and liquid cooling plates in power electronics due to its outstanding properties. It offers an excellent combination of good thermal conductivity, low weight, and high corrosion resistance, making it ideal for various cooling applications. The thermal conductivity of aluminum is approximately 200 W/mK, which, although lower than that of copper, is still sufficient to efficiently dissipate the heat generated in electronic components. The low weight of aluminum makes the entire cooling structure lighter, which is particularly advantageous in applications where weight is a critical factor, such as in aerospace or mobile devices. Another significant advantage of aluminum is its natural corrosion resistance. This property arises from the formation of a thin but dense oxide layer on the surface, which protects the material from further oxidation and corrosion processes. This makes aluminum especially suitable for use in liquid cooling plates, where it often comes into contact with cooling liquids such as water or glycol-based solutions. Compared to copper, which is prone to corrosion and often requires an additional coating, aluminum provides a low-maintenance and durable solution.
Additionally, aluminum is generally more cost-effective than other materials with high thermal conductivity, such as copper. This cost saving plays an important role, especially in the production of large quantities or projects where cost is a decisive factor. Aluminum is also very easy to process and offers high flexibility in manufacturing, enabling the creation of complex geometries and customized designs for specific cooling requirements.
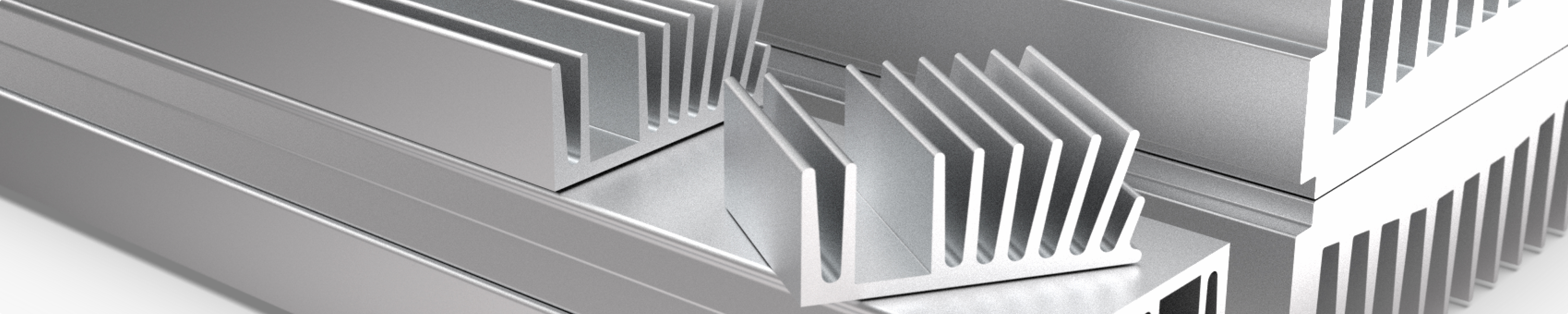
Material Alloy & Application
For the production of air heat sinks and liquid cooling plates, various aluminum alloys are used, each offering specific advantages. Extruded alloys such as EN AW 6060 (thermal conductivity approx. 200 W/mK) and EN AW 6063 (thermal conductivity approx. 200 W/mK) are characterized by their excellent processability and surface quality, making them ideal for heat sinks with complex fin structures or thin walls. These alloys also offer high corrosion resistance and good mechanical properties, making them highly versatile. For applications requiring higher mechanical demands or more complex geometries, cast alloys such as EN AW 6082 (thermal conductivity approx. 180 W/mK) and EN AW 5083 (thermal conductivity approx. 120 W/mK) are often used. These alloys offer higher strength and are very malleable, enabling the realization of challenging heat sink designs. EN AW 6082 is known for its high strength and good machinability, while EN AW 5083 exhibits excellent corrosion resistance in marine environments, making it particularly suitable for use in damp or aggressive settings. Another important material for heat sinks is the EN AW 1050A alloy (thermal conductivity approx. 230 W/mK), which is distinguished by its high purity and is especially used in deep-drawn or flow-pressed heat sinks. This alloy offers exceptionally high thermal conductivity, making it ideal for heat sinks with complex geometries and high thermal efficiency requirements. Additionally, EN AW 1050A is very ductile, facilitating the production of heat sinks through methods such as deep drawing or flow pressing without compromising mechanical stability. Using this alloy enables the production of thin-walled, high-performance heat sinks that are both lightweight and cost-efficient. Rolled plates made from alloys such as EN AW 6082 (thermal conductivity approx. 180 W/mK) and EN AW 5754 (thermal conductivity approx. 130 W/mK) are used when particularly homogeneous material structures and precise mechanical properties are required. They allow for precise machining and are ideal for applications where tight tolerances and high surface quality are critical.
The choice of the appropriate alloy always depends on the specific requirements of the application, whether in terms of mechanical strength, thermal conductivity, or corrosion resistance. Overall, aluminum, with its versatile properties and wide range of available alloys, provides an ideal basis for developing efficient, cost-effective, and durable heat sink and liquid cooling plate solutions. These characteristics make aluminum an indispensable material in modern power electronics, enabling the realization of high-performance cooling concepts for a wide variety of applications.