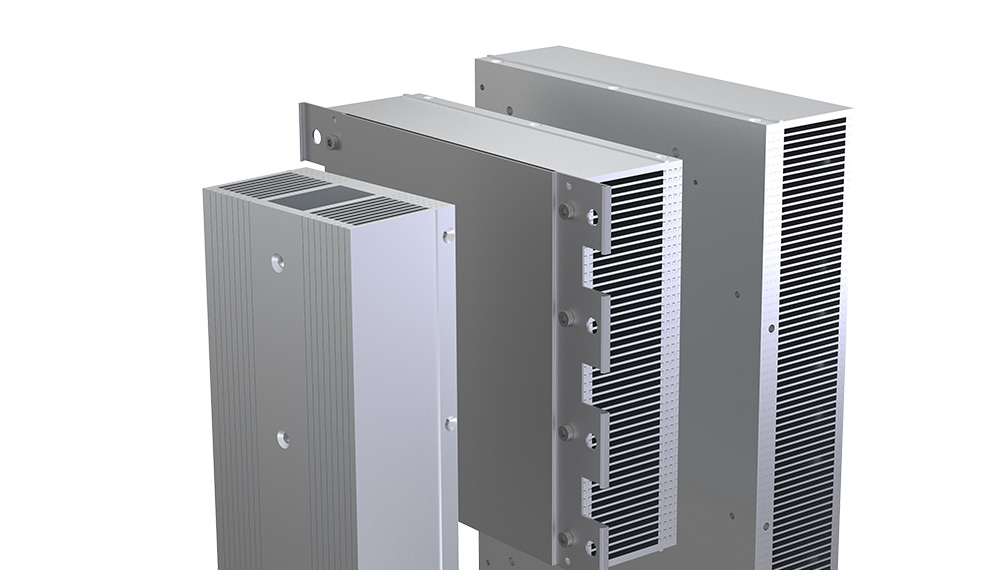
Welding
Welding plays a crucial role in connecting various materials, especially aluminum, copper, or stainless steel, to ensure optimal sealing as well as heat dissipation properties. The variety of welding techniques allows for meeting different requirements for strength, precision, and efficiency.
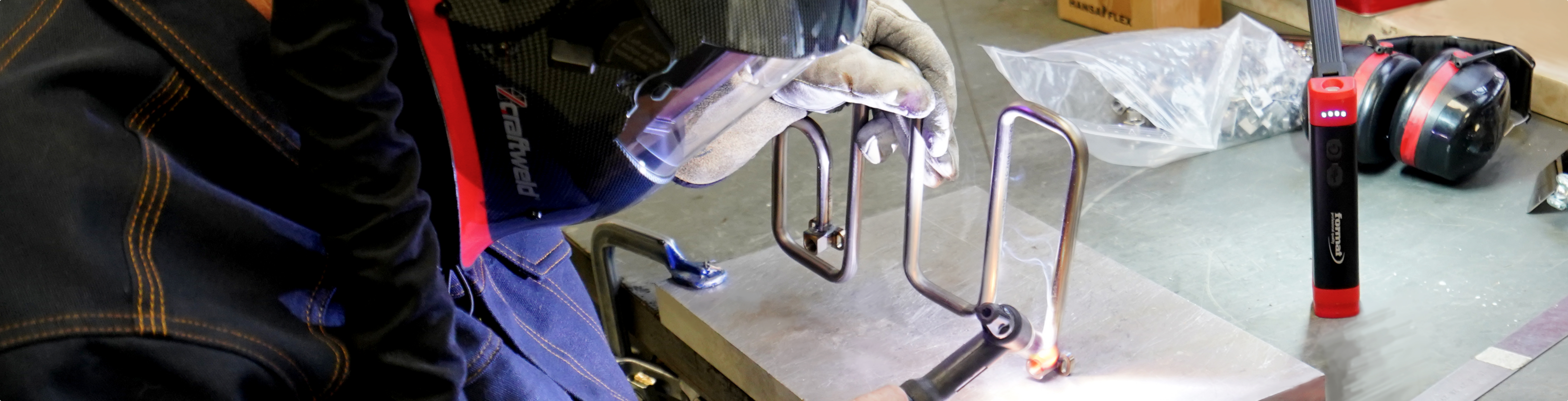
Laser Beam Welding
Laser welding is a high-precision welding technique used particularly in the manufacturing of liquid coolers. In laser beam welding, a focused laser beam is directed onto the workpiece to fuse the materials together. This method offers several advantages, making it particularly suitable for demanding applications in liquid cooling technology. One outstanding feature of laser welding is its ability to concentrate high energy on a small area. This enables precise control of the heat-affected zone and minimizes thermal expansion effects in the surrounding areas. This precision is particularly important for achieving stringent flatness requirements. Laser welding also provides high welding speeds, reducing production times and increasing efficiency. Moreover, it produces narrow, deep-penetrating welds with minimal deformation, leading to enhanced structural integrity. In liquid cooler manufacturing, laser beam welding allows the precise joining of materials such as aluminum or copper.
Thermal Performance & Stability
Copper pipes provide even more effective heat dissipation due to their high thermal conductivity, while aluminum pipes are preferred for their low weight and good corrosion resistance. The choice of material depends on the specific application requirements, such as desired thermal conductivity, corrosion resistance, or weight. In production, pipe pressing offers high flexibility, as different pipe geometries, lengths, and diameters can be easily adapted and integrated into the heat sink. This enables the creation of customized liquid cooling plates for varying performance requirements and spatial constraints. This flexibility is particularly advantageous in the development and production of prototypes or small series, where rapid adjustments and optimizations are required.
Overall, pressing technology for inserting pipes into liquid cooling plates provides an extremely effective and economical method for manufacturing high-performance cooling solutions. It combines excellent thermal performance with high mechanical stability, while also enabling flexible, cost-efficient production that meets the demands of modern power electronics.