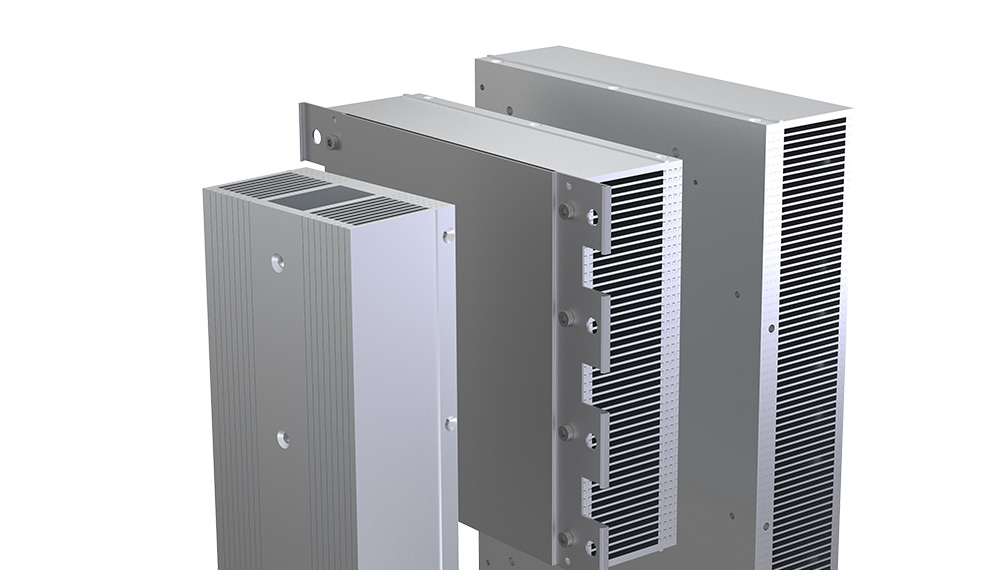
Surface Refinement
Surface refinements for air and liquid coolers improve corrosion resistance and thermal conductivity, increasing the lifespan and efficiency of the heat sinks. Refinements provide additional protection and optimized performance.
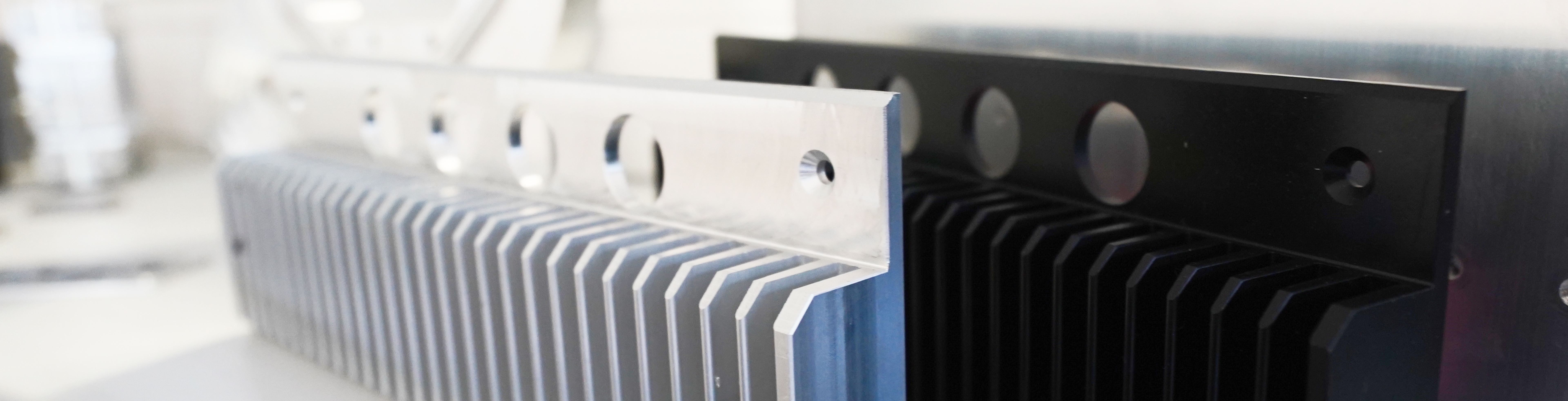
Anodizing
Anodizing is a proven surface refinement process for aluminum heat sinks in power electronics. This electrochemical treatment creates a protective, durable oxide layer that shields the material from corrosion while improving thermal and electrical conductivity. This process enhances the heat sinks’ resistance to environmental influences and chemical stress, significantly extending their lifespan. An additional benefit of anodizing is improved thermal conductivity. The controlled oxide layer optimizes heat dissipation, increasing the efficiency of the heat sinks. Simultaneously, the insulating property of the layer provides protection against short circuits, ensuring safe use in complex electronic systems. Beyond functional advantages, anodizing also offers an aesthetic upgrade for heat sinks. By coloring the anodized surface, unique designs can be realized that are not only visually appealing but also support the branding of the end product. Anodized heat sinks are widely used in power electronics, such as inverters, LED lighting, and high-power transistors, offering a cost-efficient solution to improve device performance and longevity.
Chromium-VI-Free Passivation
Chromium-VI-free passivation is a modern, environmentally friendly process for surface refinement of aluminum heat sinks in power electronics. A thin conversion layer is formed, providing excellent corrosion protection and enhancing the adhesion of subsequent coatings without using environmentally harmful chromium-VI. This sustainable alternative meets the strict requirements of RoHS and REACH regulations, ensuring safe and eco-friendly surface treatment. Heat sinks with chromium-VI-free passivation are characterized by high resistance to environmental influences, improved thermal conductivity, and increased lifespan. They are ideally suited for applications in power electronics, such as inverters, LED lighting, and high-power transistors. The process offers a reliable and sustainable solution to optimize the surface quality and functionality of heat sinks, contributing to enhanced efficiency and lifespan of electronic devices.
Chemical and Electrolytic Nickel Plating
Chemical and electrolytic nickel plating are highly effective surface refinement processes for heat sinks in power electronics. In chemical nickel plating, an even nickel layer is applied without external current through a chemical reaction, providing excellent corrosion resistance and high wear resistance. Electrolytic nickel plating, on the other hand, uses an electrolysis process to create a dense and adhesive nickel layer that optimizes the electrical and thermal conductivity of the heat sinks. Both methods effectively protect against oxidation and mechanical influences, improving the lifespan and performance of the heat sinks and making them ideal for demanding applications such as inverters, LED lighting, and high-power transistors. Moreover, nickel-plated surfaces offer excellent adhesion for further coatings and provide an appealing, uniform appearance. Nickel plating is thus an optimal solution for enhancing the functionality and durability of heat sinks in modern power electronics.
Copper Coating
Copper coating is a proven process for surface refinement of heat sinks in power electronics, where an even copper layer is electrolytically applied. This layer significantly improves thermal and electrical conductivity while providing effective corrosion protection. Thanks to its excellent conductive properties, the copper-coated surface is ideal for applications requiring a direct connection between the heat sink and electronic components. Copper coating enables SMD soldering processes directly on the heat sink, optimizing thermal coupling and mechanical stability of the components. This leads to enhanced heat dissipation and increased efficiency in critical applications such as inverters, high-power transistors, and LED lighting. Furthermore, the copper layer provides an excellent base for additional coatings and refinements, enhancing the versatility and adaptability of heat sinks in modern power electronics.
Gold Coating
Gold coating, applied on a nickel base, offers excellent corrosion resistance, optimal electrical conductivity, and minimized contact resistance. Gold-plated heat sinks are ideal for applications requiring high reliability and precise signal transmission, such as high-frequency technology and telecommunications. The NiAu coating also allows SMD soldering processes directly on the heat sink, ensuring efficient thermal coupling and stable mechanical connections of electronic components. This significantly improves heat dissipation and performance in critical applications like inverters and high-power transistors. The golden surface not only provides excellent functionality but also adds a high-quality, aesthetically pleasing appearance to the heat sinks.
Nickel-Tin Coating
Nickel-tin coating is an effective surface refinement process for aluminum heat sinks in power electronics. A durable layer of nickel and tin is electrolytically applied, providing excellent corrosion protection and high wear resistance. This coating combines the benefits of both metals, improving thermal and electrical conductivity of the heat sinks, thereby significantly enhancing their performance in applications such as inverters, LED lighting, and high-power transistors. The nickel-tin layer is characterized by a uniform, smooth surface that serves as an optimal base for additional coatings and refinements while also ensuring an attractive, aesthetic appearance. Thanks to its strong adhesion and resistance to chemical and mechanical stresses, this coating is ideal for sustainably increasing the lifespan and efficiency of heat sinks in modern power electronics.
Powder Coating
Powder coating is a highly effective process for surface refinement of aluminum heat sinks in power electronics. A special powder is electrostatically applied to the cleaned surface and then baked at high temperatures, forming a uniform, robust protective layer. This coating provides excellent corrosion protection, high mechanical resistance, and improved thermal conductivity, significantly enhancing the efficiency and durability of the heat sinks. Powder-coated heat sinks are resistant to environmental influences, chemicals, and mechanical stresses, making them ideal for demanding applications in areas such as inverters, LED lighting, and high-power transistors. Additionally, powder coating offers a wide range of design possibilities in terms of color and surface texture, allowing for individual adaptation to the design of the final product. This environmentally friendly process, which uses no solvents, ensures sustainable and cost-efficient refinement of heat sinks, offering an excellent combination of functionality, aesthetics, and protection.
Nano Coating Using the SOL-Gel Process
Nano coating using the SOL-Gel process is an innovative technology for surface refinement of heat sinks in power electronics. A nanoscale layer is applied to the surface, providing outstanding protection against corrosion, chemical influences, and mechanical stresses. The SOL-Gel process enables precise control of coating properties, creating a highly durable, ultra-thin layer that does not impair the thermal and electrical conductivity of the heat sink. Due to its minimal thickness, the original surface structure is preserved, optimizing heat dissipation efficiency and allowing seamless integration into complex electronic systems. The nano coating can be customized to produce hydrophobic, oleophobic, or antistatic properties, significantly enhancing the performance and lifespan of heat sinks in applications such as inverters, LED lighting, and high-power transistors. Additionally, the process is environmentally friendly and enables uniform coating of complex geometries, greatly enhancing the versatility and functionality of heat sinks in modern power electronics.