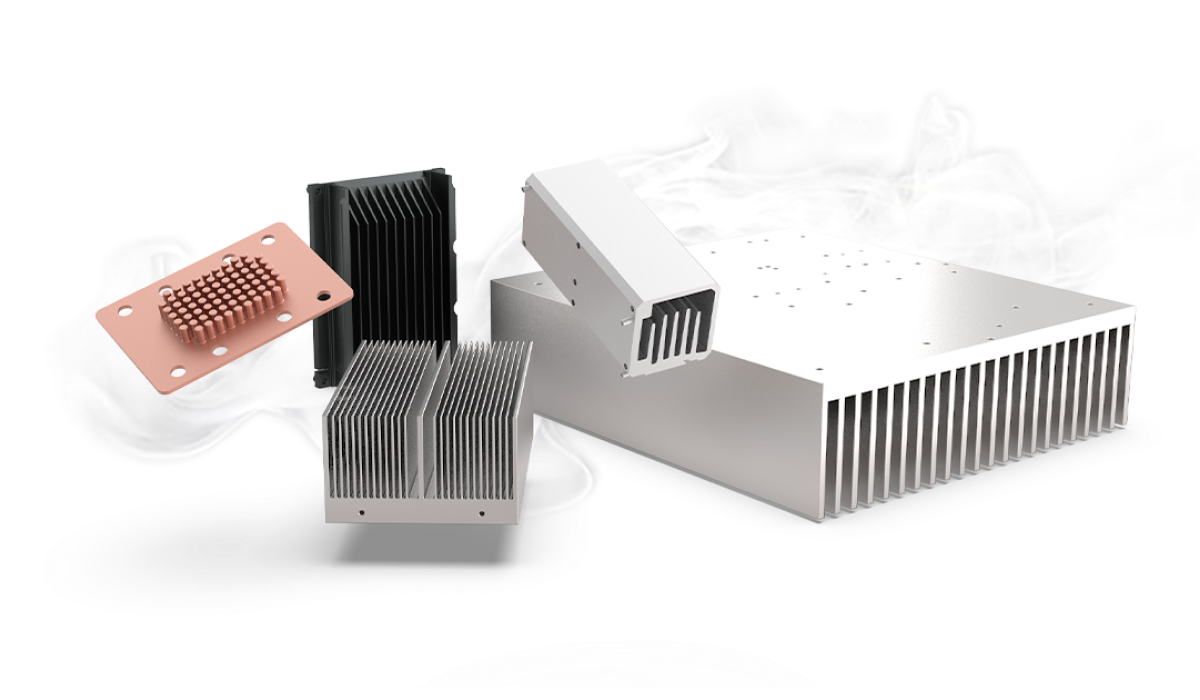
Liquid Cooler
Liquid Coolers for Data Centers
The cooling of data centers is becoming increasingly important. Due to increasing digitalization, data centers require significantly more powerful technologies for higher storage and processing capabilities. The resulting increased heat load caused by the general rise in power losses is a priority for hyperscale, enterprise, edge, colocation, and other data centers.
In the past, convective cooling systems, i.e., conventional air coolers, were sufficient, but now liquid cooling systems are increasingly being used. Only in this way can the rise in power demands be managed. Besides the liquid coolers themselves, the development and design of the coolant distributors are equally important to achieve optimal cooling performance.
Coolant Distribution Units (CDUs) are systems that enable efficient liquid cooling in a data center at the row or rack level. CDUs circulate coolant in a closed-loop system to cool racks, chassis, blades, or even down to the processors and memory.
In data centers where space saving is crucial, CDUs eliminate the need for large heat sinks, fan modules, and other components required in air-cooled systems, creating additional space in a server rack to further increase power density. Thanks to their flexibility and adaptability, CDUs are the best option for liquid cooling in data centers.
There are two main types of CDUs:
• In-Rack CDUs: Small units that can be integrated directly into a single server enclosure and distribute coolant to a series of servers or other heat sources.
• In-Row CDUs: Larger, freestanding units designed for higher heat loads in a row of server enclosures.
Support During Implementation:
One of the biggest challenges in implementing a liquid cooling system is ensuring the coolant loop is optimally filled and all air is removed from the system. Excess air can accumulate around the pump, reducing the lifespan of components within the loop.
While CDUs typically have small built-in pumps for adding extra coolant, corrosion inhibitors, or other additives, these are often too small for the initial system fill.
For large networks requiring a high volume of coolant, external pumps can be used to move the coolant efficiently through the system. This not only saves valuable space inside the server since a permanent pump is not needed but also shortens the time required to fill the system for initial operation. A larger pump also ensures no air remains in the system, preventing damage to sensitive components.
Commissioning:
Once a liquid cooling system is installed, it must be connected to the IT rack and the facility as a whole to minimize potential issues. CDUs should be designed and tested to be leak- and condensation-free for years. However, it is important to prepare for rare emergencies, such as a system leak.
If a system leak occurs, the CDU must be immediately notified to shut off the pump before the coolant can damage sensitive components. Additionally, the CDU must not only detect the leak but also pinpoint the exact location for a quick resolution.
Depending on the CDU design, there are various ways to detect and prevent leaks. Built-in humidity and temperature sensors ensure data centers operate below the dew point, reducing the risk of condensation on system lines. CDU lines are also insulated with inert neoprene to prevent moisture buildup in case condensation occurs.
System architects use wire sensors and pressure sensors to measure moisture and pressure for leak detection. Leak detection films can even instantly identify the location of a leak in various parts of the coolant loop. These methods can be mixed and adapted depending on the CDU design and installation location.
Maintenance:
Coolant distributors require regular preventive maintenance throughout the system’s lifecycle to check for flow losses, pump lifespan, power supply operation, and coolant quality.
Filters, pumps, and power supplies can be proactively replaced based on a scheduled maintenance plan or due to changes in flow rates or performance. To monitor coolant quality while it flows through the loop, LEDs can be installed in custom light trays along clear segments to quickly detect foreign particles or quality degradation. If coolant needs to be replaced or refilled, or additives such as corrosion inhibitors are required, issues should be resolved promptly.
The most effective approach is to have a competent team of thermal management experts oversee data center liquid cooling from an integrated perspective to extend system lifespan, improve overall reliability, and reduce total maintenance and repair costs.
Author: Benedikt Lausberg
Related Posts
Nanocoating of Heat Sinks
Innovative Nanocoating: Transparent, corrosion- and chemical-resistant protection for metals, water-repellent, heat-resistant up to 200°C.Published on 15.11.2024Read moreNeglect the Rth Value When Selecting Your Heat Sink
When selecting a heat sink for your system, there are several factors to consider. If you search for “heat sink selection,” you will likely encounter...Published on 15.04.2024Read more
Expand Your Know-How
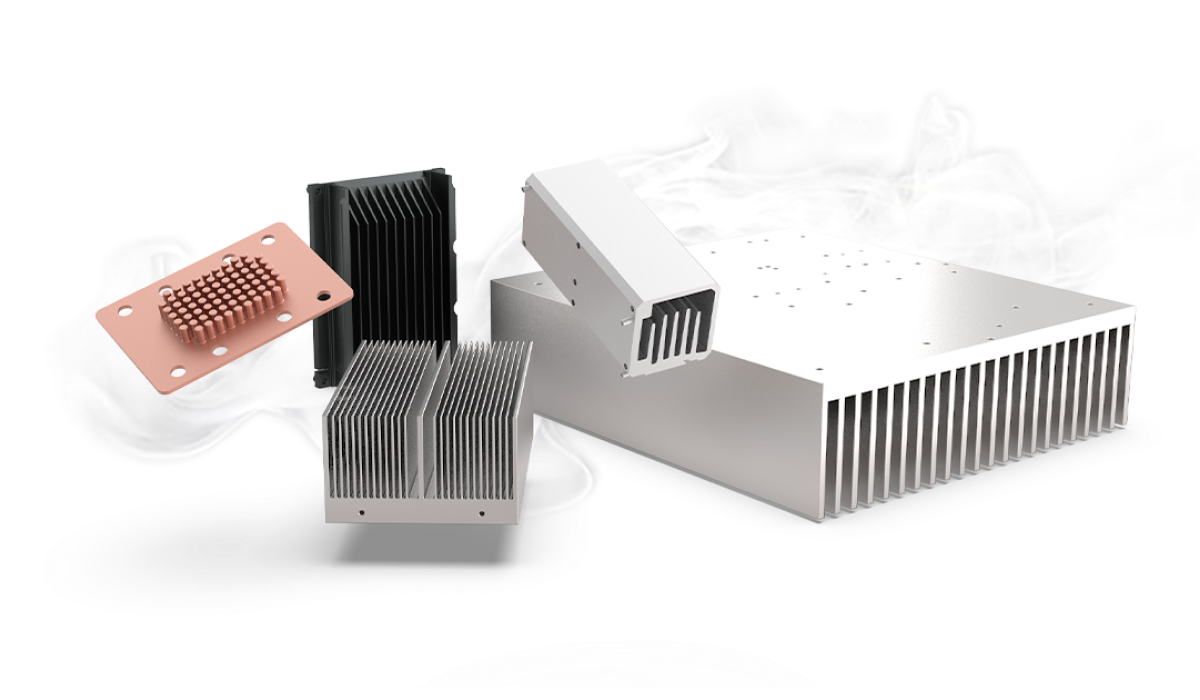
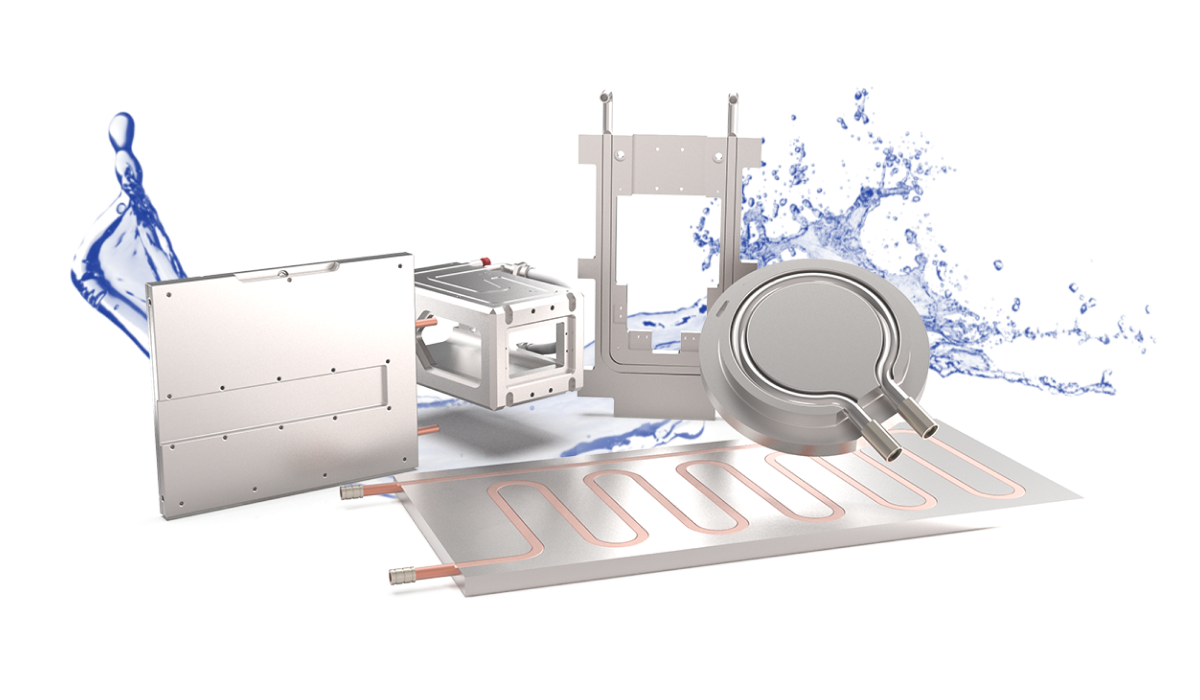
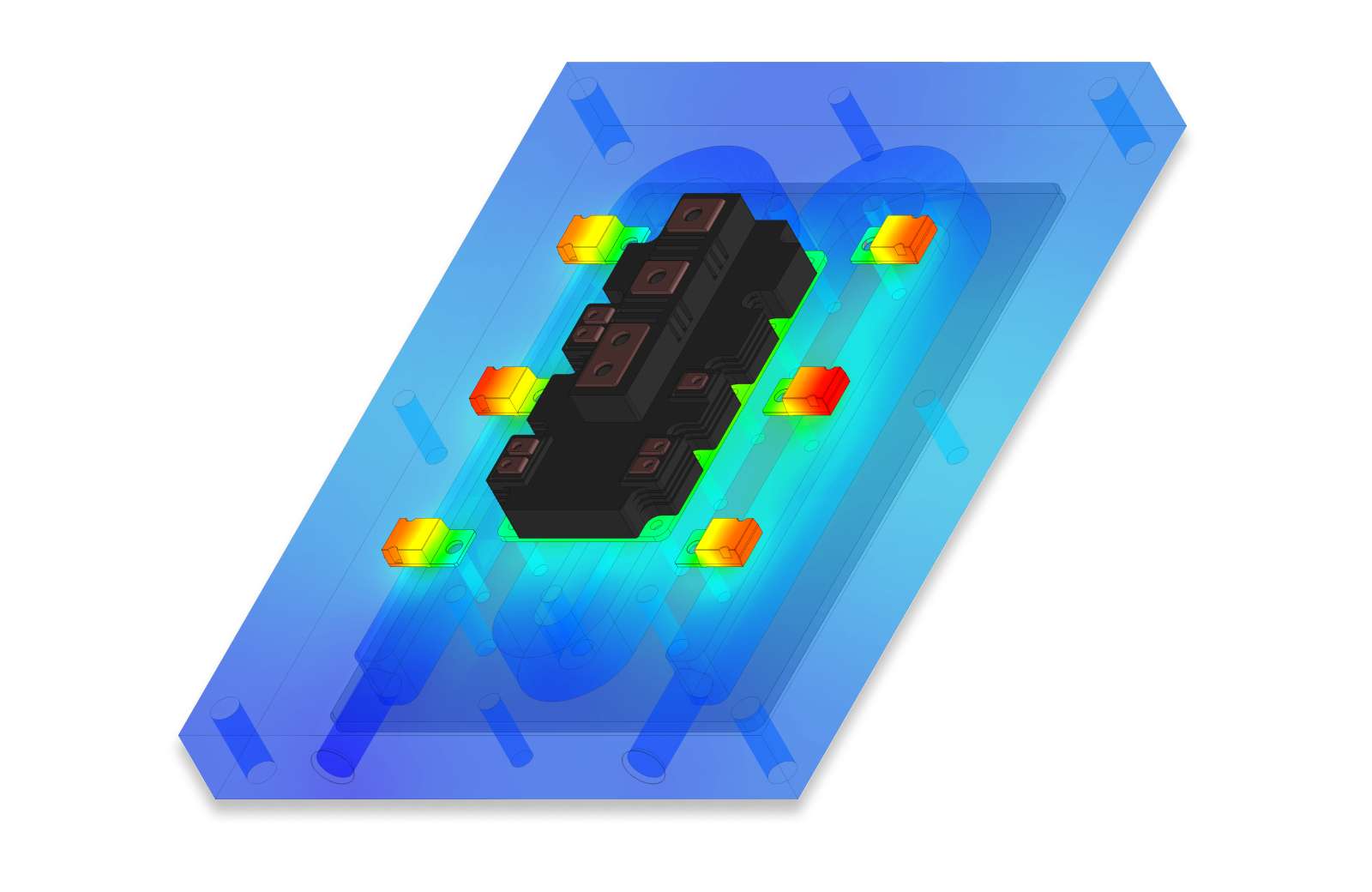