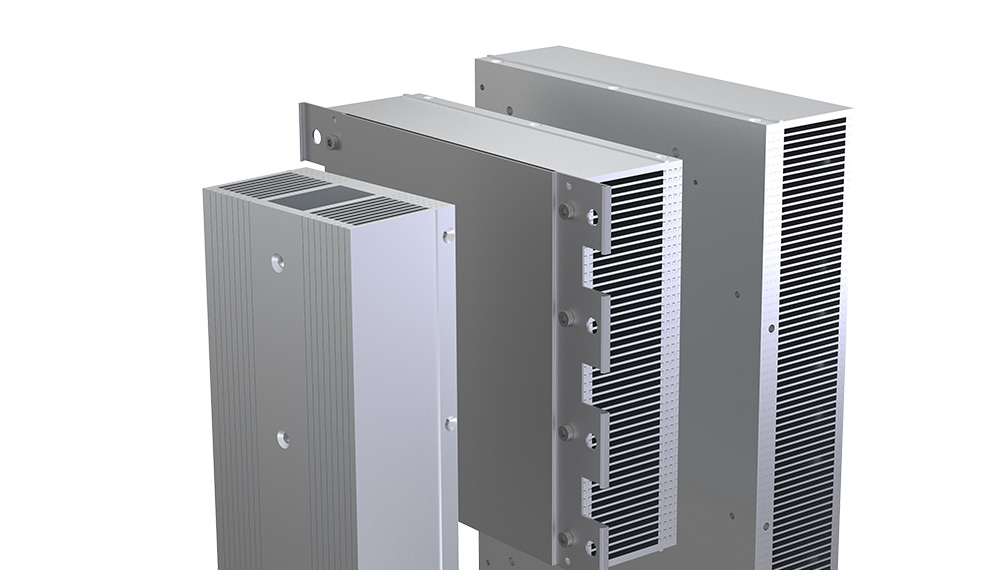
Adhesive Bonding
In the manufacturing of heat sinks and liquid cooling plates, the application of adhesive bonds as an alternative to traditional welding and soldering methods is gaining increasing importance. Adhesive technologies enable the efficient bonding of various materials such as aluminum, copper, and composites.
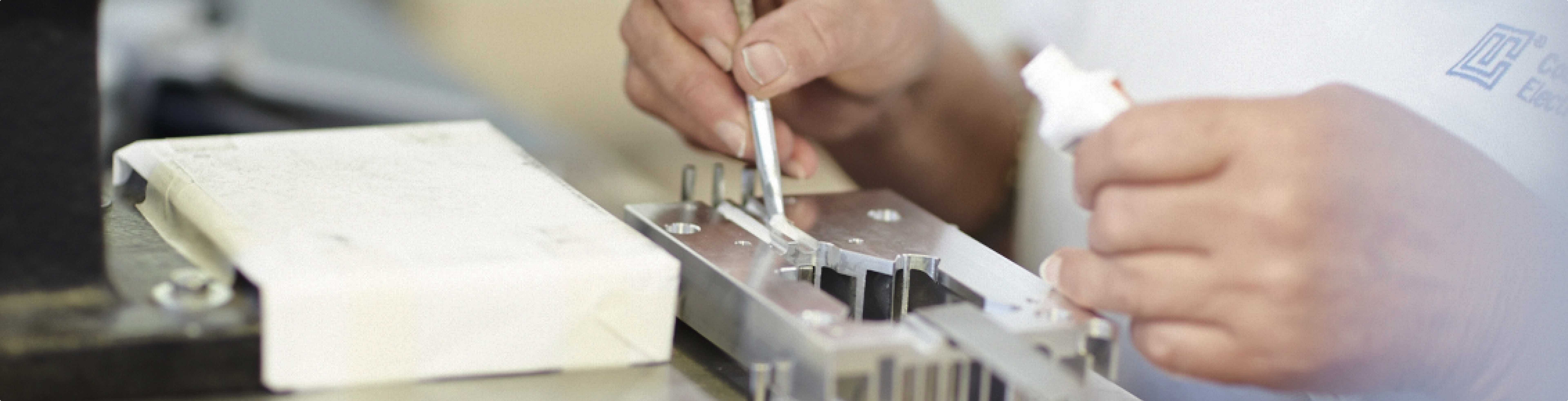
Technology & Requirements
Adhesive bonds offer uniform stress distribution, minimizing cracks, deformations, and material fatigue, which is particularly advantageous for liquid coolers and cooling plates. Adhesive technology allows for the secure bonding of materials with different thermal expansion coefficients, such as aluminum and copper, which could otherwise be damaged by thermal stresses during welding or soldering. Adhesive bonds flexibly compensate for these differences, ensuring a durable, load-bearing connection that is especially important in high-performance applications such as power electronics, automotive, and industrial electronics. Additionally, adhesive bonding enables the integration of sensitive electronic components or sensors, as adhesives cure without high temperatures and do not cause metallurgical changes to the materials.
Another advantage of adhesive bonds in liquid coolers is the ability to bond large and complex surfaces uniformly, leading to improved heat transfer between the bonded components. Specially developed thermally conductive adhesives optimize thermal properties and support efficient heat flow between materials. This significantly enhances heat dissipation efficiency, which is particularly important in high-performance applications such as inverters, power electronics modules, and LED heat sinks.
Advantages & Comparisons
Furthermore, adhesive bonds offer excellent sealing functions, preventing the ingress of liquids or contaminants, thereby improving the tightness and longevity of the cooling system. Compared to welding and soldering methods, adhesive bonds can be easily automated, enabling cost-efficient and precise production. Modern dispensing systems ensure uniform and reproducible application, increasing process reliability and product quality. This not only reduces production time but also costs, especially in series production and mass production of liquid coolers and cooling plates. Additionally, adhesive bonding offers high design flexibility, allowing for the creation of complex and delicate structures without additional mechanical connections. This is particularly advantageous in the manufacturing of thin-walled liquid coolers, where low weight and high stability are crucial. While deformations or melting can occur during welding or soldering, the shape and integrity of the components remain fully intact during adhesive bonding, improving the thermal and mechanical performance of the entire cooling system. Another key advantage of adhesive bonding is its environmental friendliness. Since no high temperatures are required, less energy is consumed, and no harmful fumes or emissions are produced, as can occur with welding or soldering processes.
Future & Automation
Many modern adhesives are also solvent-free and comply with strict environmental standards, making them an environmentally friendly and sustainable alternative for the manufacturing of heat sinks and liquid cooling plates. Combined with the ability to securely and permanently bond sensitive materials such as aluminum and copper, adhesive bonding is a forward-looking technology in cooling technology. It enables the production of high-performance and durable cooling systems that meet the increasing demands for efficiency, reliability, and sustainability. Adhesive technologies offer an innovative solution for the manufacturing of liquid coolers, which, due to their flexibility, ease of automation, and high efficiency, are an optimal choice for modern power electronics.
The advantages of adhesive bonds – from improved heat transfer and sealing to easy integration into automated manufacturing processes – make them an indispensable technology in the development and production of modern heat sinks and liquid cooling plates.