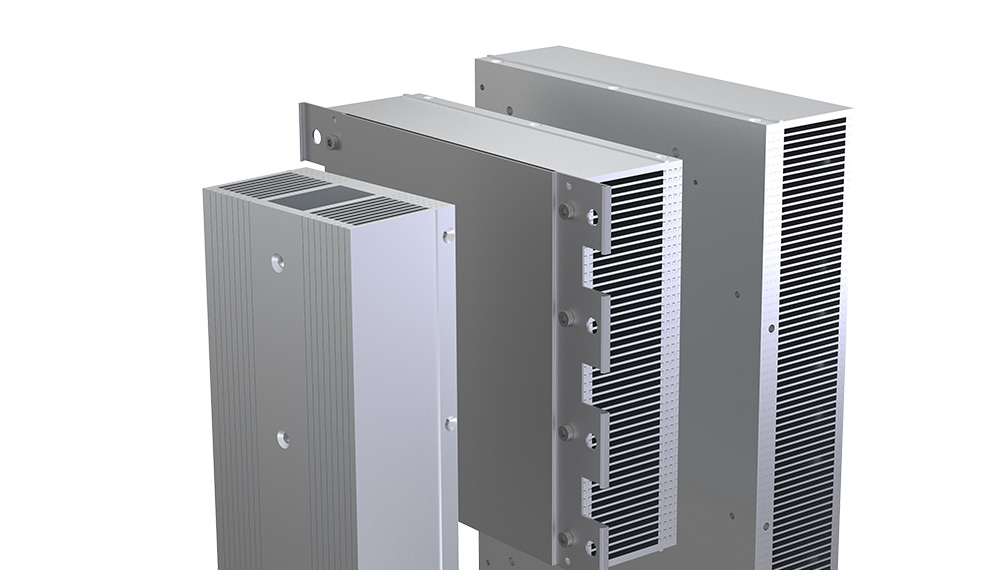
Leak Testing
Every liquid cooler is tested for its tightness. The exact requirements and test procedures can be defined together and range from the standard leak test to the documented helium leak test or pressure drop test.
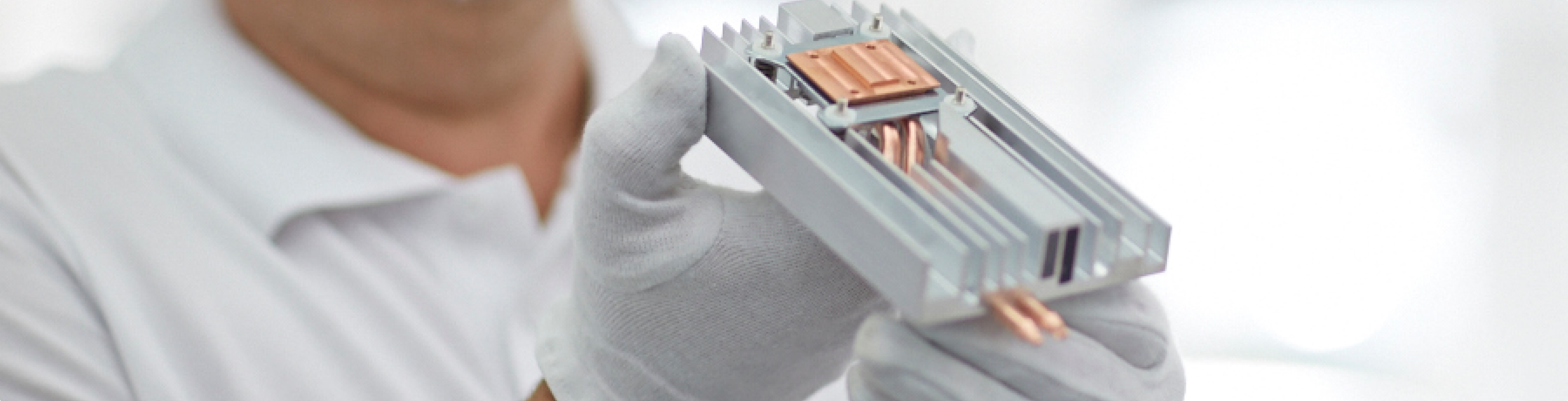
Test Procedures
Bubble Leak Test
The bubble leak test is an indispensable tool in quality assurance. A test procedure that helps companies ensure the integrity of their products. By detecting leaks early, costs can be reduced and customer satisfaction increased.
This simple yet effective technique is often used in various industries, including the food, pharmaceutical, and automotive industries. By identifying leaks, companies can ensure that their products meet the highest quality standards. The object to be tested is first coated with a soap solution. Then pressure is applied to the object to ensure that air or gas can escape. Bubbles form at the points where there are leaks, which need to be fixed. This method is ideal for checking the joints of different materials and seals.
Pressure Drop Test
A pressure drop test is a common procedure to check the tightness of components and systems. A defined pressure level is built up in a closed system and monitored over a certain period of time. If the pressure drops during the test, this indicates leaks. The pressure drop test is used in many industries to ensure that products, such as cooling systems or pipelines, are tight and functional. This method offers a reliable and precise way to detect leaks early and ensure the quality of the products before they are put into use.
Helium Leak Test
The helium leak test is a highly precise method of leak testing, often used for liquid coolers. Since liquid coolers in many applications require an absolutely tight construction to prevent the escape of coolants, reliable leak detection is crucial. In the helium leak test, the liquid cooler is either filled with helium or surrounded by it, while a special leak detector detects even the smallest amounts of escaping gas. Due to the small molecule size of helium, even microscopic leaks can be detected, ensuring the safety and functionality of the cooling systems. This method offers the highest precision and ensures the quality and reliability of the liquid coolers.
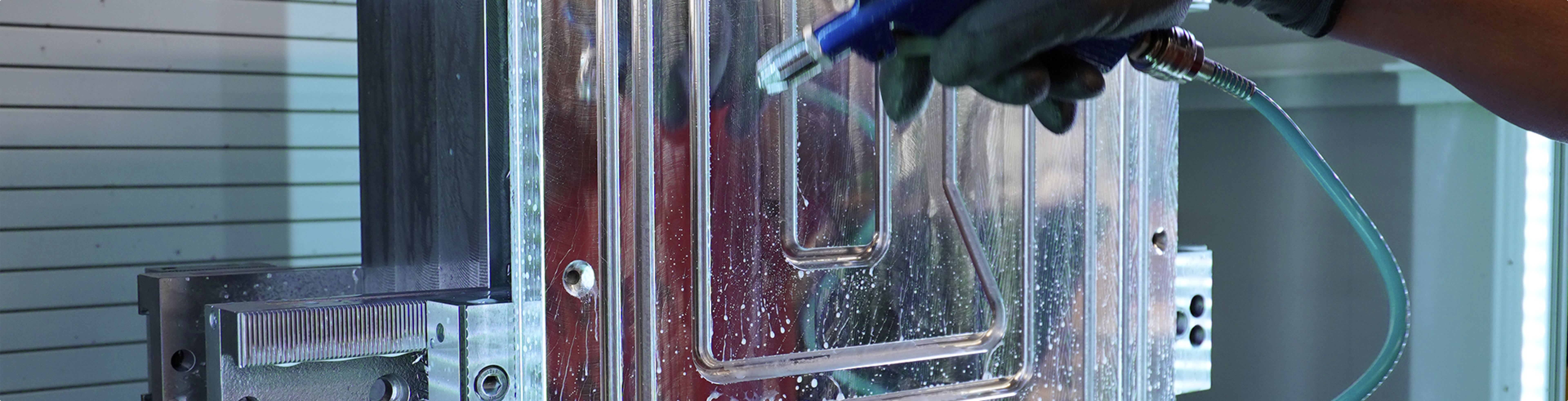
Parts Cleaning
The cleaning of heat sinks and liquid coolers is an important step to ensure the optimal functionality and lifespan of the components. During production and processing, contaminants such as dust, oils, fats, or machining residues can remain on the surfaces, impairing thermal conductivity and reducing performance. Thorough cleaning removes these residues and ensures that the heat sinks or liquid coolers dissipate heat efficiently.
Special procedures such as ultrasonic cleaning, chemical baths, or high-pressure rinsing are often used for cleaning, tailored to the materials and construction. Especially for liquid coolers, which have fine internal channels and structures, thorough cleaning is crucial to prevent blockages or deposits that could impair the cooling circuit. A clean surface and a free cooling circuit are essential for the long-term efficiency and reliability of the cooling systems.